In the giant crusher of an Australian iron ore mine, under the snowplow tracks of an Antarctic research station, and on an oil drilling platform in the African desert, a special steel is facing extreme challenges far beyond imagination. Wear-Resistant Steel Plates, the "armor" of modern industrial civilization, have built a strong wall against wear with their unique material science and process wisdom.
Image Source:699pic.com
1. The industrial epic of the material revolution
The birth of Wear-Resistant Steel Plates is itself the product of a breakthrough in material science. In 1882, British metallurgist Robert Hadfield accidentally discovered that adding manganese to steel can significantly improve wear resistance, thus giving birth to the first generation of Wear-Resistant Steel. This material, known as "devil steel", was used on tank tracks in World War I, showing amazing battlefield survivability.
Modern wear-resistant steel plates have evolved into various forms:
High manganese steel: contains 10-15% manganese, and the surface hardens rapidly under strong impact, suitable for crusher jaw plates
Low alloy wear-resistant steel: forms carbides by adding elements such as chromium and molybdenum, and the hardness can reach HB500-600
Composite wear-resistant plate: the base layer uses low-carbon steel to ensure toughness, and the surface is inlaid with ceramic particles or hard alloy
Laboratory tests show that the wear resistance of high-quality Wear-Resistant Steel Plates is 20-30 times that of ordinary carbon steel. In a friction test simulating mining conditions, a certain brand of Wear-Resistant Plates had a wear loss of only 0.8mm after 2000 hours of continuous operation, equivalent to a loss of 0.004mm per day.
2. The ultimate solution for extreme working conditions
In the Escondida copper mine in Chile, dozens of tons of ore hit the cylinder lining like a torrent in the 12-meter-diameter semi-autogenous mill. After using Hardox Wear-Resistant Plates produced by Swedish SSAB, the equipment life was extended from 8 months to 3 years, saving more than 2 million US dollars in annual maintenance costs.
The battlefield of wear-resistant steel plates is far more than this:
Construction machinery: The mixing blades of concrete mixer trucks have a lifespan increased by 5 times after using Wear-Resistant Steel
Agricultural machinery: The wear rate of harvester blades when cutting straw is reduced by 70%
Energy equipment: The ability of oil drill pipe joints to resist mud and sand wear in deep-sea drilling is increased by 3 times
The XAR series of Wear-Resistant Steel developed by ThyssenKrupp in Germany can even withstand the shooting of 7.62mm rifle bullets and are used in military explosion-proof vehicle bodies.
3. The technological code of process evolution
The process of producing Wear-Resistant Steel Plates can be called the art of material engineering. On the 5000mm wide and thick plate rolling mill of Shagang Group, the 1200℃ steel billet is rolled 7 times, and the grains are refined to 1/10 of the diameter of a hair. In the key heat treatment link, the quenching + tempering process is adopted to make the steel plate obtain a dual-phase structure of martensite + bainite.
Technological innovations continue to emerge:
Laser cladding: laser sintering tungsten carbide particles on the surface of the steel plate to form a millimeter-level wear-resistant layer
Plasma spraying: spraying ceramic powder onto the surface of the substrate, with a bonding strength of 60MPa
3D printing: through the accumulation of metal powder layer by layer, wear-resistant parts with complex shapes are manufactured
The "Super Wear-Resistant Steel" developed by Japan's JFE Steel uses nano-scale carbide dispersion strengthening technology to keep the material at a high hardness of HB480 at a low temperature of -40°C.
4. Competitive landscape of market game
The global Wear-Resistant Steel Plate market presents a three-legged trend: Sweden's SSAB, Germany's Dillingen, and Japan's JFE occupy the high-end market, while China's Hegang, Baowu, and Shagang are rapidly rising in the mid-end market. According to McKinsey statistics, the global Wear-Resistant Steel Plate market will exceed US$12 billion in 2025, of which China will contribute 40% of the increase.
The price system shows a clear gradient:
Ordinary wear-resistant plate: 8,000-12,000 yuan/ton
Imported high-end plate: 20,000-30,000 yuan/ton
Special process plate: 40,000 yuan/ton or more
It is worth noting that Chinese companies have achieved breakthroughs in subdivided fields: the NM500 wear-resistant plate developed by Anshan Iron and Steel has been successfully applied to the key components of the Hualong One nuclear power project; the graphene-enhanced Wear-Resistant Steel developed by Hesteel and the Chinese Academy of Sciences has a 45% increase in laboratory wear resistance.
5. Technological singularity of future evolution
Nanotechnology is rewriting the performance boundaries of Wear-Resistant Steel Plates. The nanocrystalline wear-resistant steel developed by the Oak Ridge National Laboratory in the United States has a grain size of only 10 nanometers and a strength three times higher than that of traditional steel. The two-dimensional material-enhanced wear-resistant steel developed by the University of Science and Technology of China showed self-healing properties in friction tests.
More profound changes come from intelligent manufacturing:
Digital twin technology realizes the full life cycle management of steel plates
Machine vision system detects the thickness of wear-resistant layer online
AI algorithm predicts the optimal heat treatment parameters
When 5G+Industrial Internet empowers steel manufacturing, and when hydrogen metallurgical technology achieves carbon-neutral production, Wear-Resistant Steel Plates are evolving from "industrial consumables" to "intelligent equipment". This evolution not only changes the underlying logic of industrial civilization, but also indicates that materials science and human wisdom will jointly write a new industrial epic.
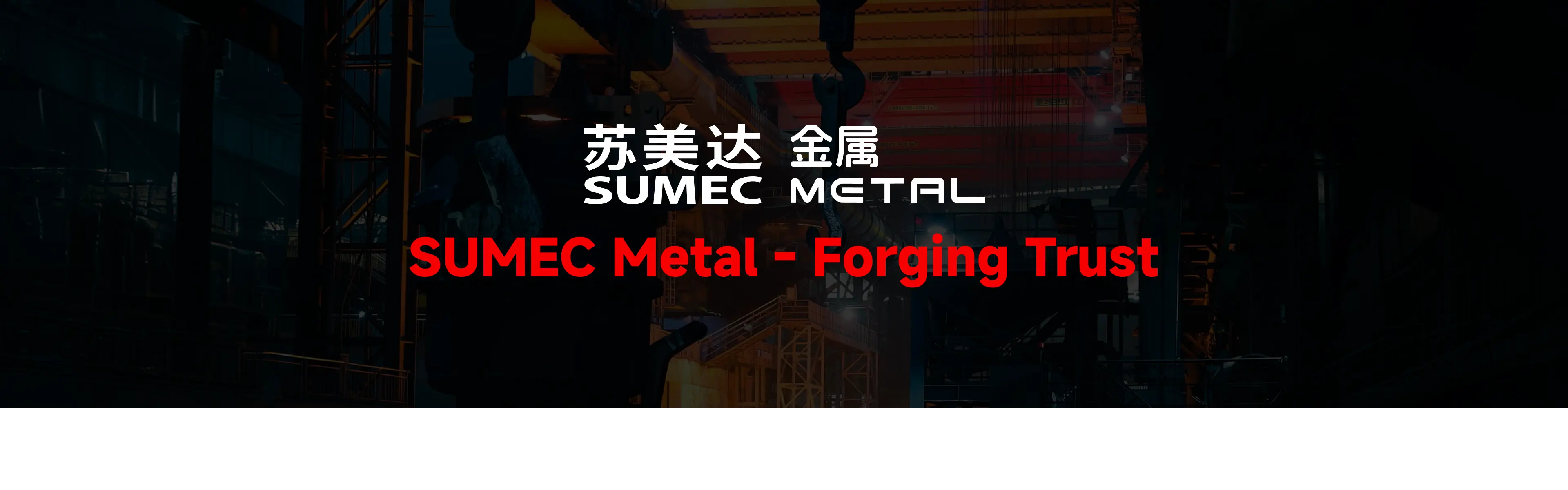