In the fields of modern home furnishings and building materials, particleboard occupies an important position due to its unique properties and diverse application scenarios. In China, the use of rubberwood to make particleboard has been a highlight in the industry in recent years.
Image Source:699pic
Rubberwood Resources and the Particleboard Industry Background
Rubberwood is widely planted in tropical and subtropical regions of Asia, and China also has a considerable scale of cultivation, especially in Hainan, Yunnan and other places. As the rubber production cycle of rubber trees ends, a large amount of rubberwood needs to find new utilization methods.
Definition and Classification of Particleboard
Particleboard, also known as chipboard or solid wood particle board, is an artificial board made by cutting wood or other non-wood plant fibers into fragments of a certain specification, drying them, mixing them with glue, hardener, waterproof agent, etc., and pressing them under a certain temperature and pressure. In terms of classification, it can be divided into three types according to density: low density (0.25 - 0.45 g/cm³), medium density (0.45 - 0.60 g/cm³), and high density (0.60 - 1.3 g/cm³); according to the slab structure, it can be divided into single-layer, three-layer (including multi-layer), and gradient structures; according to water resistance, it can be divided into indoor water-resistant types and outdoor water-resistant types. When using rubberwood to make particleboard, different classification criteria will be selected for production according to different usage scenarios and performance requirements.
Process of Making Rubberwood Particleboard
Preparation Stage: The rubberwood raw materials are cut into wood chips by a chipper, and the wood chips enter the wood chip silo for temporary storage. Subsequently, the wood chips are sent to a flaker to be processed into flakes, and the flakes enter the wet flake silo to prepare for subsequent processes. This process ensures that the raw materials can be processed into a suitable form for better combination with adhesives later.
Gluing Section: The core and surface flakes enter the corresponding glue mixers respectively. At the same time, the glue and other additives measured according to the formula are injected into the glue mixers. In the glue mixers, the flakes and the glue are fully mixed so that the glue evenly wraps the surface of the flakes to form glued flakes. The choice of adhesive and the control of the gluing amount directly affect the bonding strength and environmental performance of the particleboard.
Laying and Hot Pressing Section: The surface and core glued flakes enter the metering bin of the laying machine through a belt conveyor and are laid out into a continuous three-layer composite slab belt on the slab conveyor. After weighing, metal detection, moisture content detection, and pre-pressing, the qualified slabs enter the continuous hot press and are bonded to form a continuous rough slab belt under high temperature and high pressure, and the unqualified slabs are recycled. The hot pressing process is the key to the formation of particleboard. Appropriate temperature, pressure, and time parameters can enable the particleboard to obtain good physical and mechanical properties.
Post-treatment Section: The continuous rough slab belt after hot pressing is successively subjected to bubble detection, thickness detection, weight detection, trimming, and cutting. The treated rough slab belt is cooled and stacked for storage and enters the intermediate storage system. These processes ensure the dimensional accuracy and surface quality of the particleboard.
Sanding and Cutting Section: The rough slab belt is made into a particleboard blank by using the sanding process to make its surface reach the required smoothness and flatness, and then it is cut and processed into the final product. This step enables the particleboard to meet the market's requirements for different specifications and appearance qualities.
Environmental Performance: Rubberwood itself is a green, low-carbon, and sustainable wood resource. In the process of making particleboard, with the wide application of environmentally friendly adhesives, such as formaldehyde-free and ENF-grade adhesives, the environmental protection level of rubberwood particleboard has been greatly improved, far exceeding that of ordinary boards, meeting consumers' demands for green and environmentally friendly homes.
Industry Development Status and Prospects
With the improvement of people's living standards and the increasing requirements for the living environment, the requirements for the quality and environmental protection performance of particleboard are also getting higher and higher. In the future, the rubberwood particleboard industry will develop in a more environmentally friendly, high-performance, and intelligent direction, continuously meeting the diverse needs of the market and having broad development prospects in domestic and foreign markets.
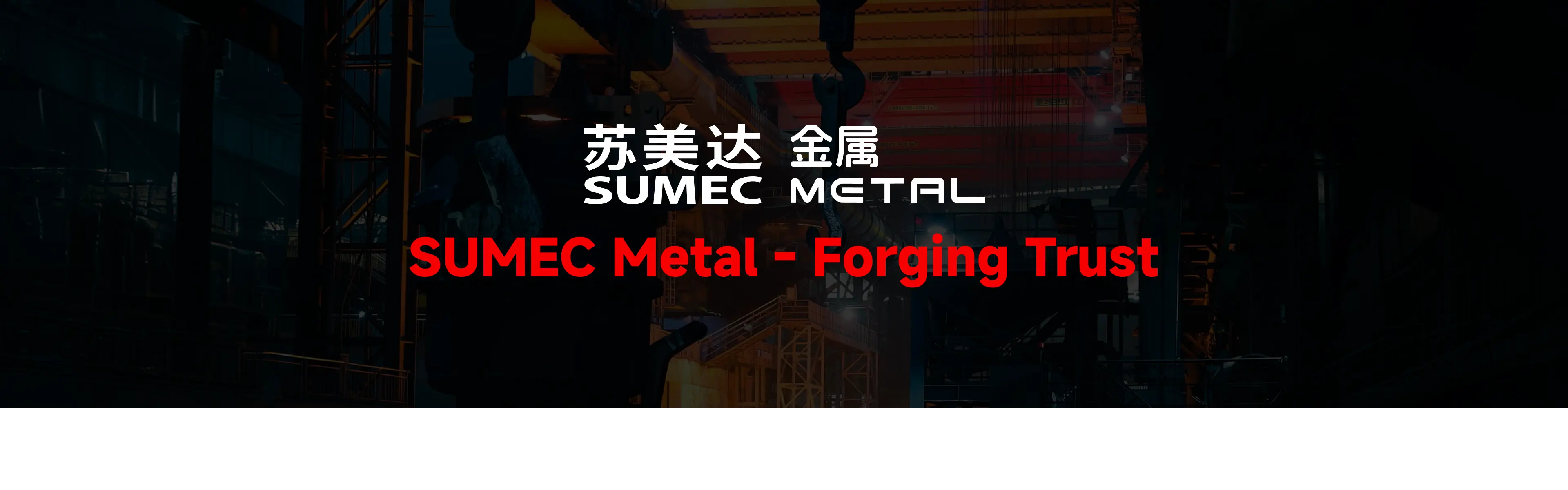