In today's highly competitive manufacturing industry, production equipment is the core asset of enterprise operation. Its performance directly affects the enterprise’s production efficiency, product quality, and market competitiveness. The after-sales maintenance of production equipment, as a key link to ensure the continuous and efficient operation of equipment, has undeniable importance. After each enterprise purchases these important resources, it will invest a lot of time and money in maintenance to use these devices for production for a longer time.
Image Source:699pic.com
Generally speaking, the after-sales maintenance of equipment covers multiple dimensions, from basic inspection to complex repair. For example, there is regular inspection. This means that technicians conduct a comprehensive inspection of the equipment at a certain cycle, which is the basic work of after-sales maintenance. In an automobile manufacturing production line, equipment maintenance personnel will carefully check the mechanical structure of stamping equipment, the welding power source and wire feeding system of welding equipment, the spray gun and paint supply pipeline of painting equipment, the conveyor chain of assembly equipment, etc. They initially judge the equipment status by observing whether there is abnormal wear or deformation on the equipment appearance, listening to whether there are abnormal noises in the equipment operation sound, and feeling the vibration of the equipment during operation. In addition, if impurities such as dust and oil accumulate on the surface or inside of the equipment, it may affect the heat dissipation of the equipment and even enter the key parts of the equipment, aggravating the wear of components. For electronic production equipment, such as circuit board manufacturing equipment, cleaning is particularly important because tiny dust particles may cause shortcircuits in the circuit. This is also something that technicians need to focus on during after-sales maintenance. They generally use professional cleaning tools and detergents regularly to comprehensively clean the equipment's shell, internal structure, vents, etc. At the same time, lubricate the moving parts of the equipment, such as chains and gears, to reduce friction, lower the energy consumption of equipment operation, and extend the service life of components. As the equipment continues to operate, some components will experience performance degradation or even damage. After-sales maintenance personnel need to replace vulnerable and aging parts in a timely manner according to the equipment operation status and the service life cycle of components. In injection molding machine equipment, components such as screws and barrels work in a high - temperature and high-pressure environment for a long time and are prone to wear. When the degree of wear affects the quality of injection-molded products, they need to be replaced on time.
In the long run, regular after-sales maintenance actually helps to reduce the maintenance costs of enterprises. When the equipment lacks maintenance, some small problems may gradually turn into serious failures, resulting in a significant increase in maintenance difficulty, an increase in the number of components to be replaced, and an increase in maintenance costs. Through regular maintenance, technicians can solve equipment problems when they are still in their infancy, and at this time, maintenance often only takes a small amount of time and cost. SUMEC International Technology Co., Ltd., as a global equipment supply chain service provider, can also provide high-quality equipment after-sales maintenane services. Through years of deep cultivation in the industry, the company has accumulated many high-quality equipment suppliers and after-sales maintenance service resources, and can provide convenient, fast and cost-effective equipment maintenance services for a large number of enterprise customers. Professional team members and a rapid response mechanism make the after-sales maintenance of enterprise equipment no longer a time-consuming and labor-intensive task. Feel free to call 4006-979-616 for specific consultation!
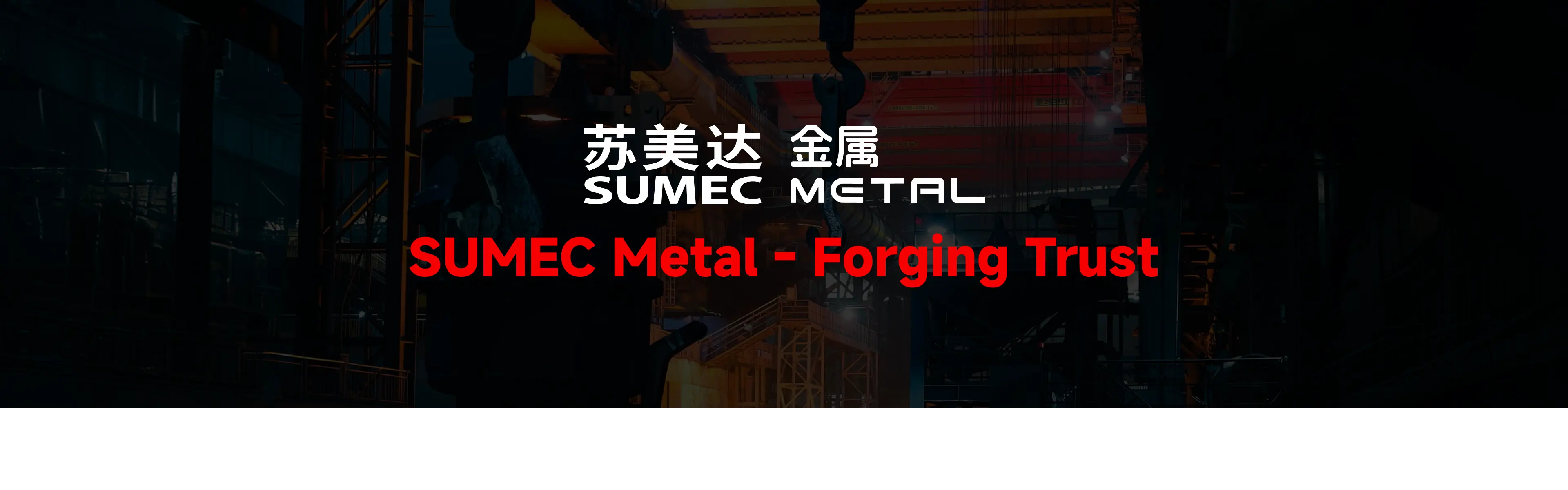